To support the processes in Picnic fulfillment centers, we developed our in-house Warehouse Management System. This system made it possible to overcome the obstacles of an off-the-shelf application. We could keep track of things happening in our warehouses, such as order picking, stock levels as well as inbound and outbound processes.
Of course, writing such a sophisticated logistics system does not happen overnight. Our approach was rather gradual: we migrated some business use cases to having more advanced technical solutions while keeping others simple — as in being managed with manual supervision and spreadsheets. As soon as the order volume became troublesome to handle, we tried to improve efficiency by streamlining the process for our shoppers and supervisors. While doing so, we found a potent tool for maximizing productivity through usability in the fulfillment centers: Guided Flows.
The rise of the Guided Flow
Think about going to a supermarket with a shopping list of 15 products. Try to imagine how long it would take you to collect everything. 15–20 minutes presumably seems reasonable, depending on how familiar you are with the supermarket. Now imagine having an app that could show you the exact location of each product. Moreover, it could also lead you to them, so you wouldn’t have to think about which shelf holds your favorite brand of hazelnut chocolate. Your shopping time would be massively reduced.
Picnic fulfillment centers look just like large supermarkets. Our shoppers pick customer orders in these supermarkets, using a device that runs an app just like the one illustrated above. This is the client app of our WMS.
The screen shows which shelf to take products from, and after scanning with a small scanner, it registers barcodes and shows the next pick. The application always shows the next action to be done, and records scan actions automatically, moving on to the following step. User errors are displayed in short, clear messages, and shoppers also have the option to resolve problems — such as reporting missing products. We call this guided picking. Order picking is our most important daily operational process, but several other ones can also be executed with the help of a guided flow. Our goal is to maximize fulfillment center productivity by implementing these as guided processes.
How we design it
Constructing a new flow starts with finding operational bottlenecks — the most critical processes in our warehouses. Steps are identified, and graphical sketches are created to visualize these steps. The UI design — app screenshots — are then added to these steps, and the flows are then implemented.
Usability is our number one priority. We believe that achieving great user experience is fundamental for creating the best warehouse application. Speeding up the way you interact with an app is essential during operation. Ideally, a shopper should not have to think about the next step. By displaying the least amount of information required for the next task, we make sure that every step is 100% clear, and the chance of errors is minimal. Spending a lot of time finding a solution to a problem when things go wrong is also out of the question. We keep the amount of problem resolution options to the minimum and also develop dashboards for warehouse supervisors to monitor processes and identify bottlenecks.
Application performance is also essential. Speed is the most important technical requirement for a guided flow. Writing fast database queries and using small payloads when communicating with the WMS backend is vital. By identifying unnecessary client-server messages and aggregating them to fewer requests, we can make sure that the network in the warehouse does not get overloaded, and the potential errors are easier to debug.
From Spreadsheets to Guided Flows
Our latest addition to the WMS application is a new flow for handling urgent replenishment. This process happens when stock is running low on a shelf, and it needs to be replenished as soon as possible to fulfill the orders that must leave the warehouse soon. This has always been quite a simple process: we collected the locations running low on stock, searched for “buffer” locations that have these products, and exported it into a spreadsheet. Warehouse supervisors were then able to ask shoppers to replenish the shelves according to these lists. A couple of database queries used to do the trick.
The issue we had is that it was just not flexible enough. Assigning and planning the workforce was still done manually, and the spreadsheets needed to be synchronized periodically. We realized what we needed to do: migrate it to a guided flow.

This is how it works: when a Shopper selects Urgent Tasks in the application, they automatically get an assignment that describes what to do. Registering the products and shelf locations happen by scanning barcodes. The app asks to move the product to the displayed location, and after scanning the destination barcode, the process is completed. After finishing the move, a new assignment can be immediately started. No need for any additional management. Bye-bye spreadsheets.
A dashboard supports the flow — an admin page to list urgent moves happening in the system to track everything transparently. Launching this new flow helps us quickly react to operational bottlenecks and better manage pressing issues with our stock. It eliminates a good deal of manual planning and possibilities of human errors.
What about Phase 2?
The future of our WMS is Guided Flows, and we believe that it has more to offer. By migrating more operational processes to these supervised actions, we increase efficiency, but there is greater potential to take productivity to the next level.
At this moment, the daily operation requires the coordinated work of warehouse supervisors to assign shoppers and find bottlenecks. This involves going through multiple dashboards and some remaining spreadsheets. With new guided flows in place, we can empower them with a single dashboard and an intelligent system that can monitor and recommend ways of operating optimally as well as resolving bottlenecks.
This way, in addition to guiding the execution of specific tasks, the automatic selection of the next — most important — task type could be the end goal. This could mean getting rid of manual planning of all daily processes — full automation in the world of manual warehouses. We are not there yet, but it is an exciting area to explore.
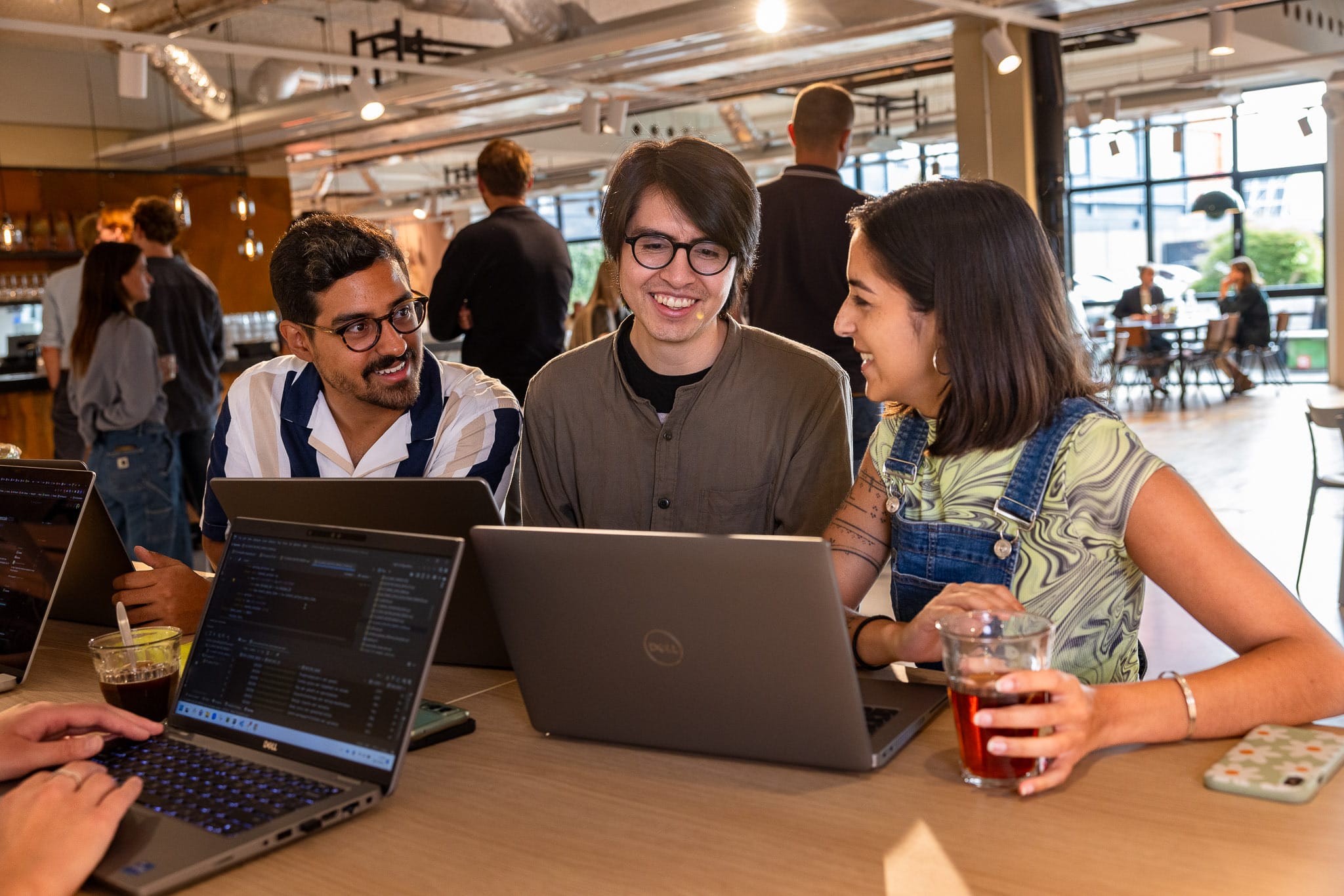